Mitigate Risk with Modernization
Reduce Business Risks Through Control System Modernization
Outdated control systems increase downtime risks, limit expansion capabilities, limit your ability to expand, provide your stakeholders with inadequate - or even inaccurate - information, and impede maintenance efforts.
Prioritizing control system modernization will decrease your production challenges and provide management with actionable information to improve performance and meet regulatory reporting requirements.
But how do you go from wanting to modernize to realizing its benefits?
Start By Asking Yourself – Does Your System Really Work?
While your control system may physically be running and putting product out the door, it may not be giving you all the benefits of a modern system.
If any of these statements sound familiar, there's a good chance you're ready for a modernization project:
-
- You frequently search eBay for equipment parts your vendors no longer support
- You struggle to make decisions because you don't have an accurate depiction of your system
- Your system is often in an alarm state that operators silence or ignore
- Your operating system no longer supports vendor patches or updates
- You rely on one person who knows the ins and outs of your system - and they're thinking about retiring
Do any of these statements ring true? Your mature or obsolete control system may already be eating into profits and posing operational risks. Learn how to mitigate these risks.
Assess the Risks of Running Your Current Control System
To begin, identify all your control system assets and how these assets communicate with other systems. For each system, assign a risk level for failure to the business.
Example:
High Risk: If a controller failure will interrupt a plant-wide utility, it should rank highly.
Low Risk: If the failure stops an individual line only, it might rank lower.
Lower Risk: If that line’s production can be shifted to other lines, it will rank even lower.
Based on the results of your risk analysis, you can discern the business and/or operational drivers for modernizing your control system.
Meet the Information Needs of All Stakeholders with Modernization
Everyone in your organization, from maintenance managers to operators to the C suite, has specific – and very different – requirements for what information they need and how they want to see it. This can make it challenging to get everyone aligned and establish a firm project scope for modernization.
What Does Your IT Organization Need?
While your control system is part of your OT network, if it's serving data to the enterprise layer, you're converging with the standards set by IT. It's important to consider the needs of your IT organization for a modernization.
What Do Your Control Room Operators Need?
A modernization effort is an excellent opportunity to ensure your human-machine interfaces (HMIs), and everything about your control room, is working well for your operators.
What Do Your Engineering Managers Need?
Your engineering team needs accurate real-time data from your control systems to make day-to-day decisions related to production schedules, equipment allocation, and product release. To effectively make these decisions, they need a single source of truth for data across all control system and device-level assets.
What Does Your Maintenance Team Need?
A modernized system is also easier for your maintenance team to support. New components suffer fewer failures; and if they do fail, spare parts and electronic documentation are readily available to support the rapid restoration of system functionality.
What Does Your C-Suite Need?
The C-Suite wants to make sure production is keeping pace and the investment in modernization is applied in the right places to maximize return on investment. For all that data to be useful, it needs to be contextualized through dashboards and reports.
Select an Integrator to Perform a FEED Study
The first step is to perform a front-end engineering design (FEED) study with a trusted system integrator partner. During the FEED study, the key stakeholders mentioned above share their concerns and requirements for the modernized system. These requirements will form the basis for the design, execution, and budget.
Determine Your Downtime Tolerance
When your system is critical for putting product out the door or supplying a key utility to your plant, the availability of your system is crucial to your bottom line. In these cases, a carefully planned and phased upgrade approach should be baked into the design. During the design phase, and not later, you need to think about your organization’s downtime tolerance to determine the extent and duration of each phase.
Consider Regulations and Codes
The design phase is also the time to consider any regulations or state or national codes your control system must comply with and how performing any upgrades will impact compliance.
Plan How to Train Operators
Consider how you will train operators on the updated system. One option we recommend involves the concurrent development of a digital twin – a digital training environment that will accelerate operator training and protect your people, processes, and equipment.
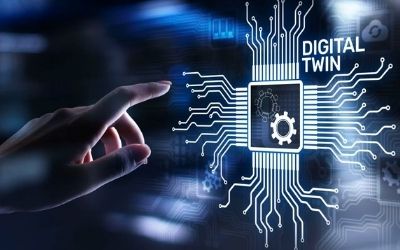
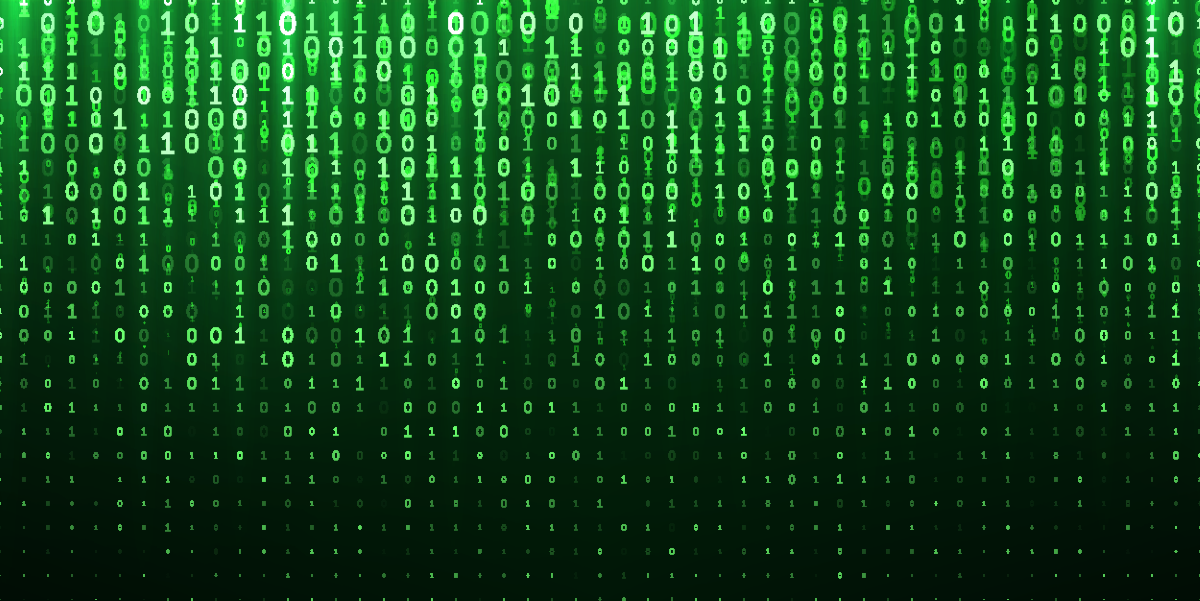