From inspecting raw materials for quality and identifying defects in finished products to performing precision measurements or rapid part verification, incorporating vision systems into your production process is a great way to boost quality and efficiency while accelerating production. While hardware and software selection for your vision system may seem paramount, there are other factors - lighting, part positioning, and testing - that are also incredibly important. In this blog, we explore how taking these factors into consideration upfront will result in optimization that eliminates many common vision system frustrations.
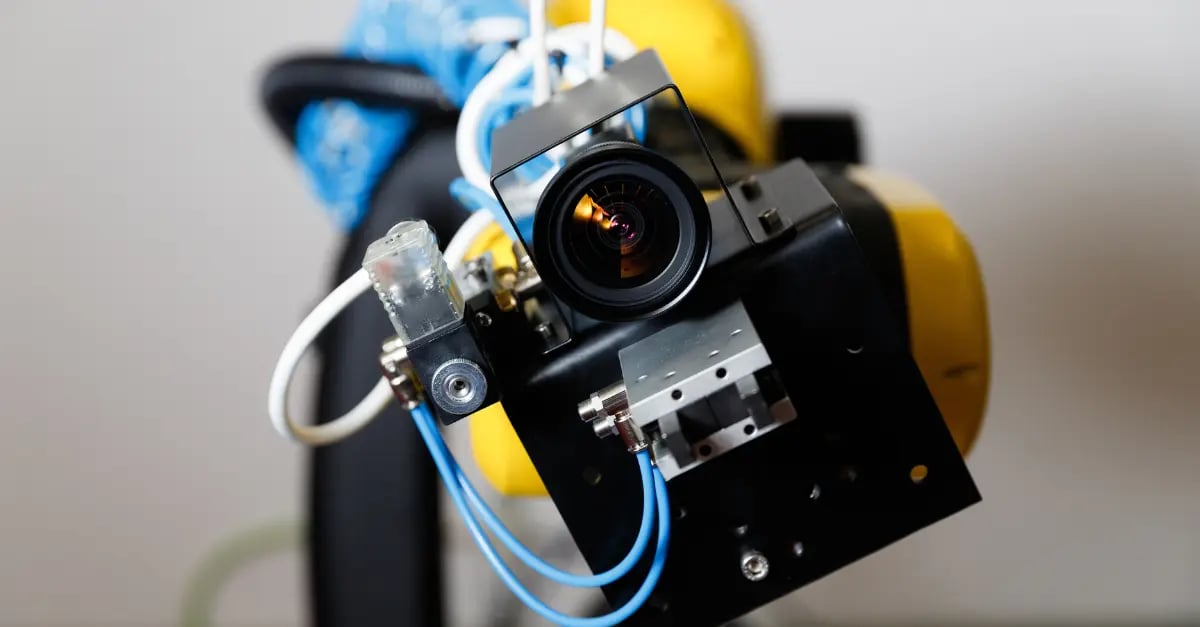
Dial in Your Lighting
Lighting design is arguably the most important component of a machine vision system. Since artificial vision can only “see” what it has been taught, its function is very different from the perception and judgments humans make on what they see. One cannot train a machine vision system to consistently recognize patterns that cannot be clearly differentiated. Distinct imaging is achieved with lighting, contrast, and consistency – challenging at best with a sole reliance on ambient lighting. Whether working with traditional vision or vision with an artificial intelligence (AI) component, variable or unpredictable lighting is problematic for machine vision systems. However, this is an issue that can be resolved.
While some initial costs may be necessary to incorporate a strategic lighting solution, this is money well spent because determining proper lighting parameters for your application is essential. Ultimately, the planning and associated costs put into a project at the beginning will result in a vision system that works consistently as designed. This will also ensure you avoid the incredible frustration that results when the ROI from a capital expenditure is zero or a newly installed system is never used because it only works sometimes.
Determine Proper Part Positioning and Required Inspection Angles
While the human eye can easily scan multiple areas of a part, a camera sensor can inspect only a single angle. Therefore, multiple camera sensors may be needed to accommodate all the necessary angles for inspection of a single part. Working with an experienced machine vision engineer early in the process to determine the number of camera sensors required will help prevent budgeting surprises.
Proper positioning of parts is also important. When parts are placed inconsistently, depending on the application, inspection may not be possible. For example, let’s imagine a cylinder. If the area of interest for inspection is located on the top disc of the cylinder, but the part has flipped and the opposite is presented to the sensor, the vision system will not be able to perform the inspection. A robotic pick and place system added upstream of the vision system may be an excellent solution for alleviating issues with part placement inconsistency.
Perform Robust Testing Prior to Commissioning
While a human can inherently see a crack in a piece of glass or a part that is improperly glued and recognize the part as defective, a vision system must be trained to know the difference between a part that is properly assembled and a flaw. To ensure that the vision system works as intended once deployed on the production line, thorough training and robust testing of the application is crucial. Training and testing should be done using the selected hardware and lighting to acquire images of the actual part and areas of interest to be inspected.
Simple? No. Doable? Yes. Choose an integrator partner such as ACE, that truly understands vision system intricacies and plans for the time required to produce a robust machine vision system.
Ready to see how machine vision can accelerate production while also boosting quality and consistency? Download our white paper on Maximizing Your Machine Vision System Investment.
Download white paper